Repeatability in manufacturing
The manufacture of products made from plastics involves a developed and tested formula based on a raw material composition that closely matches the processing parameters of a specific production line. Any structural changes to the line necessitate the introduction of new processing parameters to ensure production repeatability. This is not different when individual batches of supplied raw materials do not meet their stated parameters, or when raw materials from multiple suppliers, often differing in quality, are used interchangeably in one established production process. In such situations, it is necessary to interfere with the processing, which can adversely affect its fluidity. Any adjustments, whether to heating zones or extrusion speeds, temporarily destabilise the process, resulting in increased energy consumption or loss of energy initially inputted. This is followed by a compromise in product quality and an increase in manufacturing costs.
A finished product is formed as a result of the interaction between its components. Alongside PVC-s and plasticiser, functional components such as thermal and UV stabilisers and various lubricants should also be mentioned. Any (even minor) change in their dosage can result in deviations from the originally intended parameters of a finished product, but the most negative effects occur when the two main components, i.e. PVC-s and plasticisers are changed too hastily.
PVC-s
The main, but not the only parameter determining the choice of PVC-s is its K-number, or viscosity index. PVC-s grains are not homogeneous in their structure, having agglomerations of chains formed into different structures that do not always respond identically to the presence of the plasticiser. Their mutual quantitative ratio and repeatability in the structure of individual grains indicate the ability of PVC-s to work with a selected plasticiser.
Based on tests carried out in our laboratories, we can conclude that the same plasticiser, at different times and with different results, can plasticise PVC-s with the same as specified K number, but sourced from different suppliers. For this reason, it is worth using proven manufacturers who will ensure high quality and repeatability of the product.
Plasticiser
The amount of the main ingredient in a plasticiser is crucial to the processing. The main ingredient is the one that has the intended reaction with the PVC-s. The greater the amount of it in the dosed volume, the less residues from the esterification process, whose presence can have a significant impact not only on the continuity and repeatability of production, but also on the subsequent viability of the finished product. The plasticiser production process that guarantees the highest quantity of the main ingredient and, importantly, quantitative and qualitative repeatability of un-reacted residues, is the continuous esterification process (more: Esterification vs. transesterification – comparison of DEHT (DOTP) production methods), and the plasticiser that meets these criteria is Oxoviflex™. This product contains min. 99.5% DOTP, which sets it apart from others and directly translates into the quality of the final product.
Drawing on comparative studies carried out at the Research and Development Centre of Grupa Azoty ZAK S.A., it can be concluded that the higher amount of unreacted residue in DOTP had a negative impact on the extrusion process, migration parameters, plasticisation time, and thermal stability and strength parameters of the final product.
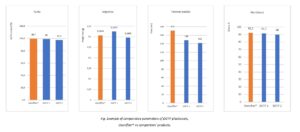
In the case of one of the competitors’ products, the higher quantity and lack of reproducibility in the quality of the unreacted residue severely affected the performance of the mix and directly impacted the viability of the final product.

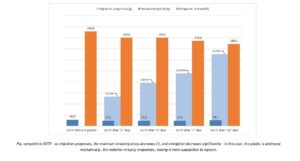
PVC-s plus plasticiser
Differences in the supply quality of the two main components are the cause of numerous production irregularities. This applies to both continuous and periodic processes, regardless of their degree of automation.
However, special attention should be paid to the case in which the semi-finished product (granulate) is made all year round and its final processing into a finished product only takes place during selected periods of batch production – i.e. the sales season. Then it is necessary to maintain a constant and repeatable quality of raw materials used throughout the year, rather than just within individual, separate deliveries. The process of PVC-s grain plasticisation does not stop at the end of production. It continues all the time, only at a slower rate. This always leads to improved plastic performance, provided that the right quality raw materials are used to guarantee a predictable and repeatable result.
Benefits of high-quality raw materials
A well-engineered production system that takes into account the consistent and repeatable quality of the raw materials used will be a predictable and recurrent process. It will help reduce costs, save time and energy and improve working conditions. All of this can increase a company’s competitive advantage while eliminating the risks associated with the unstable quality of the final product.
Do you have a query or problem relating to the processing of plasticised PVC? Send us a message!
Author:

Boris Fleites- Jończyk
Oxoplast™ Products Processing Coordinator/Business Unit Oxoplast™ / Grupa Azoty ZAK S.A.